Thermosetting polyester powder coating for aluminum profile
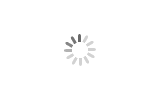
- Guangdong, China
- 600 Tons per Month
Thermosetting polyester powder coating is the most used of all powder coatings in the worldwide market. Polyester's offer a broad application field and many different chemistries including: Polyester/TGIC (triglycidyl isocyanurate); Polyester/TGIC-free; Super-durable Polyester and Polyester Hybrids.
A variety of Thermosetting polyester powder coating is provided by us at industry leading prices. These have superb flow and finish which impart brightness to the painted object. Apart from that, Thermosetting polyester powder coating also has superior mechanical properties like temperature resistance and corrosion resistance. Thermosetting polyester powder coating is available in many colors and in gloss, matt and texture finishes.
Thermosetting polyester powder coating is specially used for the coating of high-grade building aluminum profile and highway guardrail.
Thermosetting polyester powder coating for aluminum profile | ||
Product Profile | Thermosetting polyester powder coating is made of high quality polyester, curing agent, additives and pigments. Varieties of high light, half light, sub light, low light, no light, metal effect, art, wrinkles, wood grain, transparent and other color products. | |
Characteristic | The coating has excellent weather resistance and chemical resistance, tight and tough film, high mechanical strength. | |
Applicability | It is specially used for the coating of high-grade building aluminum profile and highway guardrail. | |
Theoretical coverage | 10-12㎡/kg,(Film thickness 60 ų ṃ, with the state of the workpiece, coating method, coating conditions, all the differences) | |
Dry storage stability | 12 months (less than 30 ℃) | |
Pretreatment | In order to achieve the ideal adhesion, it is recommended to use yellow chromate or green chromate to pretreat the aluminum before coating according to ISO / dn50939 standard. It is recommended to use deionized water for the last water cleaning, and dry it in a drying oven not higher than 90 ℃ to ensure the best adhesion and achieve the best durability. | |
Curing process | 1. Low temperature curing 160 ℃ @ 25min (MT) | |
2. Conventional curing 180 ℃ @ 15min (MT) | ||
3. Rapid curing 200 ℃ @ 10min (MT) | ||
Construction method | Electrostatic and friction gun spraying, manual and automatic. Metal flash powder can only be applied with electrostatic coating, and arts and crafts powder is recommended to use automatic gun spraying to ensure uniform color and appearance effect. | |
Main technical specifications | ||
Item | Test standard | Index |
Gardner60 º gloss | ASTMD523,ISO2813,GB/T9754-18 | Gloss between 5-95% as per customer requirements |
Scribble adhesion | ASTMD3359,ISO2409,GB/T1185-98 | Grade 0 |
Bending test of shaft bar | ASTMD522,ISO1519 | 3mm |
Impact resistance | AS3715 2.8,GB/T1732-93 | 30-50kg.cm |
Cupping test | ISO1520 | 4-7MM |
Pencil hardness | GB/T6739-98 | 1H-2H |
Salt fog resistance | ASTMB117-87,GB/T1771-91 | The maximum scratch corrosion after 1000H test is 1mm |
Heat and humidity resistance | ASTMD2247-87,GB/T17740-89 | After 1000h, the coating has no effect on the light loss |
QUV artificial accelerated aging | 1000h | No powdering, light retention > 80%, color change less than munsel1 |
Resistant to 10% HCI | 240h | No bubbles, no surface damage |
Resistant to 10% NaOH | 240h | No bubbles, no surface damage |
Water resistant | 1h | No bubbles, no peeling |